Clark are delighted to partner with a leading food manufacturer to recruit a Quality Assurance Supervisor. This is a fantastic opportunity to join a dynamic team and develop your career.
Job Purpose: Development and maintenance of the Quality and Food Safety systems to customer, third party standards, and ensuring adherence to relevant legislation
Reports to: Quality Manager
Location: Naas, Co Kildare
Key Responsibilities:
Responsibilities associated with this role include, but are not limited to:
• Maintain the supplier management process with detailed specification, risk assessment,
audit, and approval records for all raw material, packaging or miscellaneous suppliers
• Travel to conduct supplier audits as necessary as part of new approval, ongoing review or in
response to issues
• Review and evaluate suppliers to give feedback on performance and quality on a frequency
that reflects their risk, size and complexity
• Manage the approval of new raw material, packaging or miscellaneous suppliers
• Keep buying team appraised of supplier behaviours / quality of service / goods as part of
review
• Implement and Maintain detailed specifications and quality standards for all finished
products, knowledge of various software programmes used by customers required (Assured,
Hamilton Grant, FIND, etc)
• Develop and maintain internal specifications for the factory
• Manage queries or complaints from customers in a timely manner, involving the wider
Technical and production teams where needed
• Travel to customers and represent the companies technical expertise when needed as part
of customer service or as part of investigations of issues
• Hold responsibility for capturing, recording ,and trending customer complaints and assisting
Quality Manager in investigations
• A Key member of the companies HACCP team, challenging processes food safety systems
and maintaining and reviewing the plan as required
• Responsible for the document control and maintenance of the Quality Management System
• Update process documentation (check sheets and procedures) as required when driven by
improvement, audit requirements, customer requirements etc
• Assist Quality Manager in implementing the internal audit programme to ensure Quality
System compliance
• Full participation in external audits for food safety and quality audits for customers,
governing bodies (BRC/ Dept of Agriculture) and other regulatory authorities
• Ensure raw material, process and finished product evaluation and verification is completed
as required within production, being part of the team helping to solve issues as they arise
• Implement microbiological, chemical and physical testing schedules in accordance with
agreed programme and budget. To include: Finished product and raw material micro,
Chemical analysis of relevant product, Daily organoleptic assessment panel
Quality Assurance Technologist
• Report non-conformances and drive root cause analysis in a timely and comprehensive
fashion, involving all relevant disciplines
• Ensure communications of customer requirements to the Operations team and ensure
compliance to KPI targets
• Carrying out investigations for customer complaints, liaising with the production /
maintenance teams as needed to find cause, agreeing actions that can be put in place to
prevent recurrence
• Management of quarantined product, ensuring product traceability and safety is maintained
• Shelf-life analysis management as required for chilled and frozen product
• Interface with NPD as required for the successful launch of new products into production
• Budget Controls - Ensure QA related costs are effectively monitored
• Responsible for maintaining records for due diligence and audit purposes
• Collating technical information to view trending and take relevant actions where required
• Champion the training and development of staff in the areas of food safety or quality
including: Induction, Hygiene & Cleaning, Basic Food Hygiene, HACCP, Allergen Awareness,
Taste Panel training (Shared responsibility with Quality Manager & Plant Manager)
• Drive and implement plant wide Process & Quality System Improvements, working with the
relevant departments to ensure multi-disciplinary approach
• Use trended data / statistical analysis from KPI’s as part of continuous improvement loop
• Implementing Quality improvement initiatives in both manufacturing and business processes
• Liaise with New Product Development team where necessary to ensure the smooth and safe
introduction of new products, lines and processes which are integrated into the QMS
Skills / Qualifications/ Experience:
• Ability to communicate effectively with and present to Customers, Stakeholders (eg DAFM),
Suppliers and Senior Management / Directors
• Understanding of Food Safety and Quality Management Systems
• Strong knowledge of food legislation, BRC Global Food Standard and specific customer
standards and Codes of Practice
• Good interpersonal and leadership skills, and the ability to react well under pressure
• Proficient in the use of MS Office tools
• Demonstrate flexibility and adaptability
• Ability to work cross functionally, meet deadlines and build effective relationships
• Ability to identify and implement improvements
• Ability to train / instruct and coach entry level and floor-based employees
• Diploma or higher in a Food Science related subject
• Lead auditor certification is preferential
• HACCP certification is preferable
• Excellent written, numerical, and verbal skills
• Numerical ability to record, interpret and analyse key process data
• Fluency in the English language
• 1 -2 years in a similar role in a FMCG or food retail environment
• Excellent written and verbal English
Please send your CV or contact our team on 045 881888
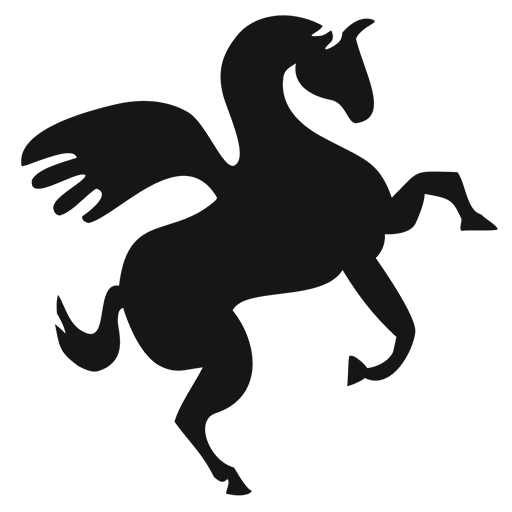
CONTACT CLARK TO APPLY
To apply for this position, fill in the form below and we will get back will get back to if you are an appropiate candidate for the role.